Milling media are the main component in the technological process of grinding materials for the production of cement, electric power, and glass and silicate products, when extracting the concentrate for metal production.
It should be noted that the price cannot be the only determinant factor for choosing a grinding media supplier. By selecting a resource, cement companies and mining companies increasingly focus on reducing the specific consumption of milling media per tone of the product produced in monetary terms, which is the optimal ratio of the specified consumption and the prices of the milling media. In order to choose the appropriate resource for grinding media, the production technology applied should be understood, as well as to understand the type of grinding media required in the specific case (engineering, grinding media material and technical parameters – hardness).
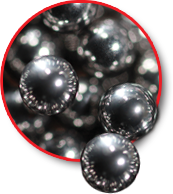
International experience shows that the use of steel grinding balls (instead, cylinders, elliptical cylinders) of high carbon steel alloys in the cement industry (for clinker milling and limestone) and the mining industry (the first, second and third stages of grinding with ore concentration provides a large economy by limiting Consumption of electricity and the consumption of electricity compared to others, the specific consumption was reduced by applying grinding balls to dry milling (clinker, bauxite, etc.) by 1.5-2 times, and wet grinding (grinding ore) – at least twice. Iron “This is expensive and is mainly used in mills where the rapid loading of the milling medium is impossible Please note that for the most efficient use, the „white” grinding media shall be equipped with the inner cylinder of the ball mill with an armored lining of The same article.
During selection, grinding media must be clearly understood for the type of milling media to be loaded into the treadmill by engineering parameters. The manufacturer usually refers to the need to use the milling media types in the mill data sheet (provided that the treadmill is fitted with a permanent shield).
In essence, grinding balls are recommended as a grinding medium for ball mills, since they have many advantages over other types of grinding modes (cylpebs, elliptical, roller):
– Improving the quality of milling. The steel grinding balls have a perfect spherical shape (no „shells”, „tail”, „holes”, etc. inherent in the cast iron grinding media). This greatly increases the contact area of the grinded material and the grinding media.
– Lack of defects in ball geometry. It leads to the process of eliminating the uneven erosion of the ball, which reduces the grinding media consumption and improve the quality of grinding.
– Reduce the cost of providing milling: improving warehouse areas, reducing additional loading time, saving electricity, etc.
During the selection of grinding hardness the media is generally repelled by the hardness (abrasive) of the material for grinding. For grinding solid materials require means of grinding steel.
The size (diameter) of the grinding media depends on the size of the mill feeder (the particle size of the material supplied to the mill) and achieved a degree of accuracy (size and percentage of material required when the ball mill is released). Typically, the size of the milling media indicates the technical documentation of the mill. If the required technological parameters are not implemented, the size of the selected grinding media is experimentally in the milling process, averaging the diameter by changing the grinding media in the mill.
In general, the process of selecting the required milling media is rather complex, because the resolution represents many of the factors mentioned above.